Meet Our Team
Service Team
Sales Team
Additional Locations
International Contact
Canada Contact
Phone
USA SALES OFFICE
Permian Operations Facility
2700 N County Road 1287, Midland,
TX 79707
855-870-2640
24 HOUR OPERATIONS/TOOL DISPATCH
855-870-2640
USA OPERATIONS FACILITY
3016 Venergy Drive
Brookshire, TX 77423
855-870-2640
Video Summary:
Related Videos
In the early days of impulse, we were spending our time developing ball drop technology. As industry leaders and being first in the race to turn a tool on, we focused all of our energy into that. Then we noticed customers doing a shift. Normally a vibration tool is around 600 meters to 2000 feet behind the bit in a relatively low torque environment. Now that customers could remotely control the vibration of the second tool, we started to see customers run two or even three tools. The tools naturally migrated up the string closer to the build section. What we didn't see coming was how much increased torque was closer to the build section. Very quickly, customers, whether they were using Impulse technology, dual tool, or systems from competitors started to see connection failures. We started to try to understand what was happening. To solve the problem we turned to the world of connections. This video demonstrates the evolution of the technology. The decades old API connection with a large taper and small ID (internal diameter) was used. Some decades ago, it migrated towards an Acme connection. The Acme connection give you more ID with the same torque rating. In 2015/2016 we needed to have even more ID when we're trying to design the inside of a tool, more importantly, we need to have more strength. When you compare the high torque, double shoulder, balanced connection to the API or ACME connection, the high torque connection gives the largest ID and the strongest connections in the industry. If you think about designing and putting things inside a connection and how much "real estate" room you have, you can obviously see that you have much more room to work with (photo 1). One of the biggest things that happened as we migrated from a single shoulder acme style connection to a double shoulder is not only the increase in torque, but how it limited failure. The old connections don't shoulder up against anything. As you apply more torque, the connection would want to keep going past the threads. The common failure from single shoulder connections was a box split. The high torque double shoulder balanced connection shoulders at the top and the bottom. So as you try to apply over torque, that connection has nowhere to go. It's housed between those two shoulders. (Photo 2) One of the challenges that's always present when when we're developing downhole tools is the rigidness of the tool. If you have a tool that's only laying out in the lateral, rigidness is not a problem. When tools are used further up the string with our multiple tool system, and we're rotating through the build section, there are extreme bending forces on the tool. Single shoulder connections don't handle cyclical bending loading as well as double shoulder connections. High Torque double shoulder balanced connections give increased torque strength, and increased ID for what we want to put inside the tool. Additionally, the tool inherently handles cyclical loading, and the bending loading that we see as we transition through build sections, or turn sections in the well bore.
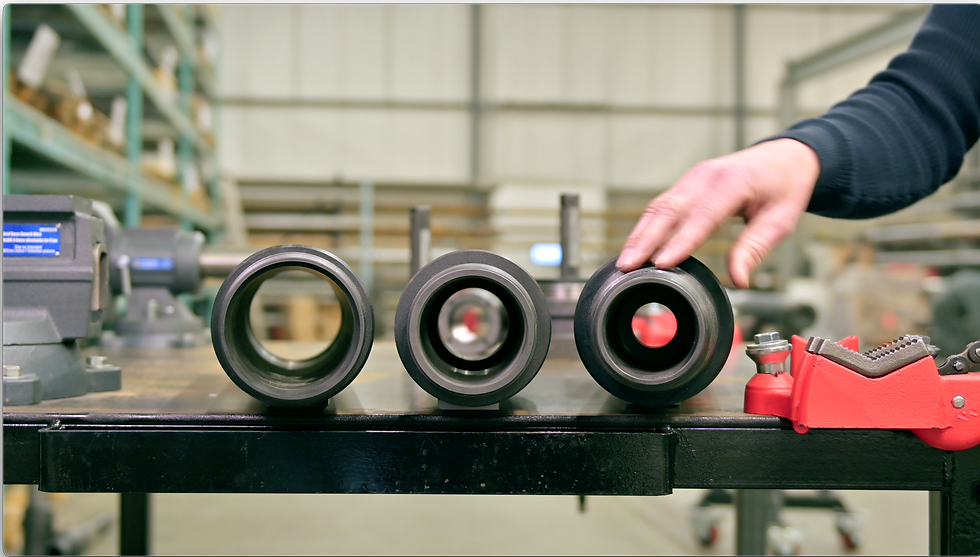
HT, ACME, and API Connections
Double Shoulder Connection
